Электродуговая и газовая сварка металлов находят широкое применение в различных отраслях промышленности и народного хозяйства. Каждый сварной шов требует проверки на соответствие необходимым стандартам, однако требования к проверке могут существенно различаться. Например, методы контроля сварных соединений трубопроводов не будут одинаковыми с подходами для проверки металлоизоляции рентгенографического оборудования.
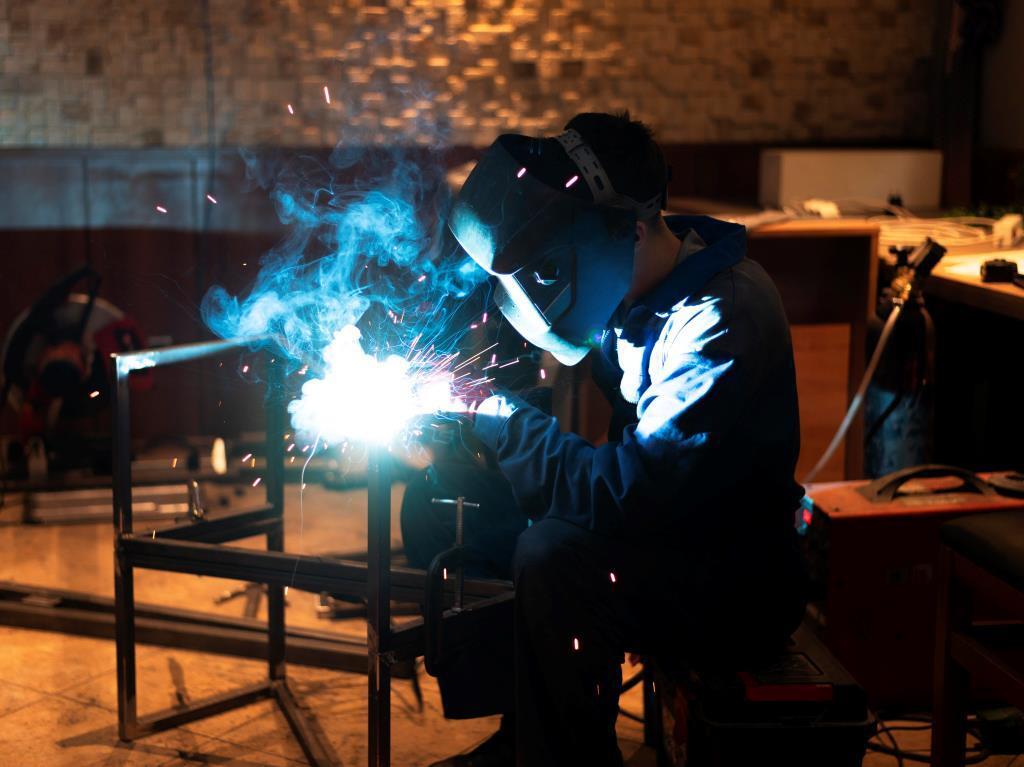
В некоторых сферах предъявляются особые требования к дефектоскопии сварных швов, включая:
- Трубопроводные системы водоснабжения, нефтегазовые магистрали;
- Изготовление высоковольтных опор;
- Машиностроение, авиационная и судостроительная отрасли;
- Строительство мостов.
Методы выявления дефектов швов могут быть разделены на два типа согласно российским нормативам (ГОСТ 3242-79):
- Разрушающие методы — такие как механические испытания, проводимые в лабораториях с использованием разрывных машин.
- Неразрушающие методы контроля (НК) — используются как в лабораторных условиях, так и на практике, непосредственно на производственных объектах. Благодаря ряду технических и экономических преимуществ, НК методы находят более широкое применение.
ГОСТ 3242-79. Соединения сварные. Методы контроля качества
В данной статье мы подробно рассмотрим особенности неразрушающего контроля сварных соединений, классификацию существующих методов и рекомендации по выбору оптимального способа контроля на промышленных объектах.
Неразрушающий контроль сварных швов
Неразрушающий контроль сварных швов включает в себя набор методов и техник, которые позволяют оценить качество сварного соединения без его разрушения или повреждения. Основная цель такого контроля — выявление дефектов, таких как трещины, поры и пустоты, которые могут возникнуть из-за неправильной сварки или использования низкокачественных материалов. Этот вид контроля применяется как в процессе сварочных работ для проверки качества соединений, так и в ходе эксплуатации конструкций, чтобы оценить их техническое состояние, безопасность и степень износа.
Согласно ГОСТ ISO 17635-2018, контроль сварных соединений осуществляется с использованием неразрушающих методов, что гарантирует соответствие изделия необходимым прочностным характеристикам. В зависимости от этапа выполнения работ, выделяют три типа контроля сварных соединений: предварительный, операционный и приемочный.
ГОСТ ISO 17635-2018. Неразрушающий контроль сварных соединений. Общие правила для металлических материалов
Предварительный контроль сварных соединений включает:
Операционный контроль, или контроль в процессе сварки, осуществляется мастерами на производстве, а выборочный контроль может проводиться независимыми экспертами. Особенно широко применяется приемочный контроль, который используется при строительных, монтажных и ремонтных работах с применением методов неразрушающего контроля, проводимых независимыми инженерами-экспертами.
Приемочный контроль осуществляется по завершении сварочных работ и включает несколько этапов проверки качества сварных соединений. Он включает внешний осмотр и измерение параметров швов, а также различные методы испытаний, такие как проверка на плотность, рентгеновское и гамма-лучевое просвечивание, ультразвуковое тестирование, магнитный контроль, металлографические исследования и механические испытания.
- Проверку параметров сварного шва, таких как длина и катет, для соответствия нормативным требованиям и исключения ошибок в проектировании.
- Оценку свариваемых материалов и заготовок, расчет и определение необходимых параметров сварки.
- Контроль квалификации сварщиков, контролеров ОТК и инженеров, которые отвечают за качество сварных соединений.
- Проверку состояния сварочного оборудования и комплектующих, используемых в процессе сварки.
Операционный контроль, или контроль в процессе сварки, осуществляется мастерами на производстве, а выборочный контроль может проводиться независимыми экспертами. Особенно широко применяется приемочный контроль, который используется при строительных, монтажных и ремонтных работах с применением методов неразрушающего контроля, проводимых независимыми инженерами-экспертами.
Приемочный контроль осуществляется по завершении сварочных работ и включает несколько этапов проверки качества сварных соединений. Он включает внешний осмотр и измерение параметров швов, а также различные методы испытаний, такие как проверка на плотность, рентгеновское и гамма-лучевое просвечивание, ультразвуковое тестирование, магнитный контроль, металлографические исследования и механические испытания.
Иными словами, неразрушающий контроль сварных соединений представляет собой набор методов, которые дают возможность выявлять дефекты в металлических соединениях без повреждения или изменения целостности изделия. Помимо этого, такие методы позволяют получить данные о структуре материала и его физических и химических характеристиках.
Согласно ГОСТ 18353-79, существует девять основных методов неразрушающего контроля, которые делятся на две группы в зависимости от типа дефектов, которые они позволяют выявлять:
Основной принцип работы методов неразрушающего контроля, использующих поля, заключается в регистрации изменений этих полей при взаимодействии с объектом. В местах, где есть дефекты, обычно происходят искажения параметров поля, что позволяет обнаружить аномалии.
- Для обнаружения наружных дефектов: магнитный, вихретоковый, оптический и методы с применением проникающих веществ.
- Для выявления внутренних дефектов: электрический, радиоволновой, тепловой, радиационный и акустический.
Основной принцип работы методов неразрушающего контроля, использующих поля, заключается в регистрации изменений этих полей при взаимодействии с объектом. В местах, где есть дефекты, обычно происходят искажения параметров поля, что позволяет обнаружить аномалии.
ГОСТ 18353-79. Контроль неразрушающий. Классификация видов и методов.
Классификация дефектов сварных соединений
Классификация дефектов сварных соединений подробно изложена в ГОСТ Р ИСО 6520-1-2012. Этот стандарт определяет общепринятую маркировку дефектов и включает официальные переводы терминов на английский язык, что позволяет составлять отчеты с едиными наименованиями, используемыми дефектоскопистами, инженерами и сварщиками в России.
ГОСТ Р ИСО 6520-1-2012 Сварка и родственные процессы. Классификация дефектов геометрии и сплошности в металлических материалах. Часть 1. Сварка плавлением
Дефекты классифицируются по различным параметрам и делятся на шесть основных групп:
Трещины и микротрещины, которые включают:
Полости, поры, усадки. Эта группа описывает различные виды пористости сварного металла, включая внутренние, внешние и сквозные поры, а также дефекты, такие как свищи и раковины, которые могут возникать при эксплуатации.
Твердые включения. Эти дефекты включают:
Несплавления и непровары. Эта группа охватывает дефекты, возникающие из-за недостаточного соединения металлов в процессе сварки.
Отклонения формы и размера. Включает дефекты, такие как подрезы, проплавы, а также классификацию протеков, прожогов и смещений.
Прочие дефекты сварных соединений. В эту категорию входят все остальные дефекты, которые не попадают в другие группы.
Эта классификация помогает систематизировать дефекты сварных соединений и обеспечивает единообразие в их определении и устранении.
Трещины и микротрещины, которые включают:
- продольные;
- поперечные;
- радиальные;
- кратерные;
- разветвленные;
- разрозненные трещины.
Полости, поры, усадки. Эта группа описывает различные виды пористости сварного металла, включая внутренние, внешние и сквозные поры, а также дефекты, такие как свищи и раковины, которые могут возникать при эксплуатации.
Твердые включения. Эти дефекты включают:
- шлаковые;
- флюсовые;
- оксидные;
- металлические инородные вкрапления и скопления;
- оксидные пленки в металле шва, что особенно важно для алюминиевых сплавов.
Несплавления и непровары. Эта группа охватывает дефекты, возникающие из-за недостаточного соединения металлов в процессе сварки.
Отклонения формы и размера. Включает дефекты, такие как подрезы, проплавы, а также классификацию протеков, прожогов и смещений.
Прочие дефекты сварных соединений. В эту категорию входят все остальные дефекты, которые не попадают в другие группы.
Эта классификация помогает систематизировать дефекты сварных соединений и обеспечивает единообразие в их определении и устранении.
Когда проводится НК сварных соединений?
Неразрушающий контроль сварных соединений проводится для оценки качества и пригодности сварных швов к дальнейшей эксплуатации. Этот контроль необходим на различных этапах, включая сварочное производство, изготовление и строительство оборудования, а также при его монтаже, ремонте и реконструкции. Кроме того, НК применяется в процессе эксплуатации объектов, в том числе по завершении установленного срока службы оборудования, работающего под избыточным давлением, а также строительных конструкций и других технических устройств. Контроль позволяет проверять соответствие параметров объекта установленным техническим требованиям и оценивать его текущее техническое состояние.
Классификация основных методов неразрушающего контроля
Не существует единственного универсального метода для выявления и фиксации дефектов сварных соединений. В промышленности применяются комбинированные подходы контроля, которые включают новейшие достижения в области приборостроения и информационных технологий. Из-за широкого разнообразия методов невозможно охватить все аспекты в одной статье, поэтому мы рассмотрим лишь наиболее популярные и часто используемые методы.
Визуально-измерительный контроль (ВИК)
Визуально-измерительный контроль является основным и первичным методом неразрушающего контроля. Он осуществляется посредством внешнего осмотра и выполнения измерений с использованием стандартных измерительных инструментов, таких как рулетка, штангенциркуль и шаблоны. Этот метод является малозатратным и позволяет выявлять внешние дефекты, включая:
Визуально-оптический метод также относится к этой категории. В нем применяются увеличительные стекла или микроскопы для более детального осмотра, что помогает обнаружить поверхностные дефекты на сварных швах.
- наличие шлака;
- металлические брызги;
- ржавчину и загрязнения;
- сквозные прожоги;
- подрезы;
- остатки флюса и другие.
Визуально-оптический метод также относится к этой категории. В нем применяются увеличительные стекла или микроскопы для более детального осмотра, что помогает обнаружить поверхностные дефекты на сварных швах.
Ультразвуковая диагностика (УЗД) или дефектоскопия (УЗК)
Ультразвуковая дефектоскопия представляет собой совокупность эхо-акустических методов, которые используются для неразрушающего контроля сварных соединений различных материалов с помощью ультразвуковых волн. В процессе применяется ультразвуковой преобразователь и дефектоскоп для обнаружения дефектов в сварных швах. Эти приборы измеряют различия в длине волн отраженных сигналов или импульсов, возникающих из-за изменений в плотности материалов или наличия пустот.
УЗД сопоставимо с рентгеновской диагностикой, использующей гамма-излучение, но обладает рядом преимуществ, таких как простота в эксплуатации и отсутствие вредного воздействия на людей в зоне контроля. Это делает ультразвуковую дефектоскопию одним из самых популярных методов проверки качества сварных соединений.
УЗД сопоставимо с рентгеновской диагностикой, использующей гамма-излучение, но обладает рядом преимуществ, таких как простота в эксплуатации и отсутствие вредного воздействия на людей в зоне контроля. Это делает ультразвуковую дефектоскопию одним из самых популярных методов проверки качества сварных соединений.
Магнитопорошковый контроль (МПД)
Магнитопорошковый контроль является эффективным методом для обнаружения как поверхностных, так и подповерхностных дефектов сварных соединений, таких как трещины, непровары, шлаковые и флюсовые включения, окисные пленки, подрезы и другие.
Принцип работы метода основан на взаимодействии магнитных частиц с неоднородными магнитными полями, которые возникают над дефектами в намагниченных объектах. Эти поля притягивают магнитные частицы, образуя индикаторные рисунки, которые отражают форму дефектов. Визуально или с использованием оптических приборов оцениваются эти рисунки, что позволяет выявить и зафиксировать дефекты.
Методика контроля:
Особенности метода: Магнитопорошковый контроль применим только для изделий с магнитными свойствами. Также возможно использование метода для объектов с немагнитными покрытиями (например, краска, лак, хром, медь, цинк и др.), если толщина покрытия не превышает 40-50 мкм. Этот метод не нарушает пригодность объекта и дает быстрые результаты, проводясь прямо на месте. Однако он не позволяет точно определить параметры дефектов, такие как их длина, глубина и ширина. Для более точной оценки дефектов комбинируется с визуально-измерительным контролем (ВИК).
Принцип работы метода основан на взаимодействии магнитных частиц с неоднородными магнитными полями, которые возникают над дефектами в намагниченных объектах. Эти поля притягивают магнитные частицы, образуя индикаторные рисунки, которые отражают форму дефектов. Визуально или с использованием оптических приборов оцениваются эти рисунки, что позволяет выявить и зафиксировать дефекты.
Методика контроля:
- Очистка поверхности от загрязнений и окалины.
- Намагничивание объекта, содержащего сварное соединение.
- Нанесение магнитного порошка или суспензии на поверхность.
- Осмотр и анализ индикаторных рисунков.
- Оценка результатов с помощью визуального осмотра или приборов.
- Интерпретация результатов.
Особенности метода: Магнитопорошковый контроль применим только для изделий с магнитными свойствами. Также возможно использование метода для объектов с немагнитными покрытиями (например, краска, лак, хром, медь, цинк и др.), если толщина покрытия не превышает 40-50 мкм. Этот метод не нарушает пригодность объекта и дает быстрые результаты, проводясь прямо на месте. Однако он не позволяет точно определить параметры дефектов, такие как их длина, глубина и ширина. Для более точной оценки дефектов комбинируется с визуально-измерительным контролем (ВИК).
Вихретоковый контроль (ВК)
Вихретоковый контроль используется для обнаружения как поверхностных, так и подповерхностных дефектов сварных соединений, таких как трещины и непровары.
Принцип действия метода заключается в анализе взаимодействия внешнего электромагнитного поля с вихревыми токами, которые генерируются в объекте контроля. При наличии дефектов в материале эти токи ослабляются, что фиксируется специальными приборами.
Методика контроля:
Особенности метода: Вихретоковый контроль может проводиться бесконтактно, но при этом зазор между датчиком и поверхностью не должен превышать 2 мм, иначе чувствительность метода снижается. Диапазон измеряемых глубин составляет от 0,5 до 5000 мм. Метод не нарушает эксплуатационные характеристики объекта и оперативно предоставляет результаты контроля.
Принцип действия метода заключается в анализе взаимодействия внешнего электромагнитного поля с вихревыми токами, которые генерируются в объекте контроля. При наличии дефектов в материале эти токи ослабляются, что фиксируется специальными приборами.
Методика контроля:
- Установка преобразователя на контролируемую поверхность для создания вихревых токов.
- Сканирование поверхности и фиксация изменений в токах с помощью прибора.
- Оценка размера и конфигурации дефектов, а также их эквивалентной площади.
- Интерпретация полученных данных.
Особенности метода: Вихретоковый контроль может проводиться бесконтактно, но при этом зазор между датчиком и поверхностью не должен превышать 2 мм, иначе чувствительность метода снижается. Диапазон измеряемых глубин составляет от 0,5 до 5000 мм. Метод не нарушает эксплуатационные характеристики объекта и оперативно предоставляет результаты контроля.
Оптический контроль
Оптический метод контроля сварных соединений основывается на способности оптического излучения проникать на небольшую глубину в непрозрачные материалы, что позволяет выявлять исключительно наружные дефекты. К этому методу также относится визуально-измерительный контроль, в ходе которого осуществляется осмотр объекта с использованием различных приборов, таких как эндоскопы, фотоаппараты-микроскопы, лупы и другие.
Как проводится оптический контроль?
В процессе работы с эндоскопом или фотоаппаратом-микроскопом осуществляется детальный осмотр сварных швов, что позволяет обнаружить видимые дефекты на поверхности материала.
Как проводится оптический контроль?
В процессе работы с эндоскопом или фотоаппаратом-микроскопом осуществляется детальный осмотр сварных швов, что позволяет обнаружить видимые дефекты на поверхности материала.
Контроль проникающими веществами (капиллярный метод)
Этот метод позволяет выявлять дефекты, которые выходят на поверхность и являются сквозными.
Этапы капиллярного метода контроля сварных соединений:
Этот метод особенно эффективен для контроля сварных соединений из нержавеющих металлов. Его преимущество заключается в простоте и скорости, а также в том, что по расположению и размерам дефектов можно определить их характер. Однако метод ограничен ручной работой и токсичностью используемых материалов, что затрудняет его автоматизацию.
Этапы капиллярного метода контроля сварных соединений:
- Подготовка поверхности — очистка с использованием инструментов и растворителей, сушка.
- Обработка дефектоскопическими материалами — на поверхность наносится индикаторная жидкость (пенетрат), которая проникает в трещины благодаря капиллярным силам. Затем излишки жидкости удаляются, и наносится проявитель (обычно порошковый), который ярко окрашивается в местах дефектов (обычно в красный или оранжевый цвет).
- Обнаружение дефектов — дефекты выявляются визуально, реже с использованием преобразователей.
Этот метод особенно эффективен для контроля сварных соединений из нержавеющих металлов. Его преимущество заключается в простоте и скорости, а также в том, что по расположению и размерам дефектов можно определить их характер. Однако метод ограничен ручной работой и токсичностью используемых материалов, что затрудняет его автоматизацию.
Электрический контроль
Электрический метод контроля сварных соединений используется для обнаружения глубинных дефектов. Он основан на изменениях характеристик электрического поля, возникающего в объекте под воздействием специальных приборов. Существует несколько подвидов этого метода, но суть их сводится к одному — в местах повреждений металла изменяется электрическое поле. Для обнаружения дефектов могут использоваться электростатический порошковый метод, который фиксирует изменения поля в зоне дефектов, или электроискровой метод, который регистрирует электрический пробой.
Недостатки метода — взаимодействие с объектом контроля, высокие требования к чистоте поверхности и зависимость от внешних факторов (например, его нельзя применять в воде, в отличие от вихретокового контроля). Однако преимуществом этого метода является возможность проведения контроля в реальных эксплуатационных условиях, где могут возникать дефекты — такие как температура, вибрации и давление.
Недостатки метода — взаимодействие с объектом контроля, высокие требования к чистоте поверхности и зависимость от внешних факторов (например, его нельзя применять в воде, в отличие от вихретокового контроля). Однако преимуществом этого метода является возможность проведения контроля в реальных эксплуатационных условиях, где могут возникать дефекты — такие как температура, вибрации и давление.
Тепловой контроль (ТК)
Тепловой контроль используется для оценки теплового состояния объектов, выявления отклонений от установленных форм и геометрических параметров, а также обнаружения дефектов, таких как трещины, пористость, расслоения и инородные включения. Метод позволяет также выявлять изменения в структуре и физико-химических характеристиках материалов, таких как теплопроводность, теплоемкость и коэффициент излучения.
Принцип работы метода основан на взаимодействии теплового поля объекта с чувствительными термометрическими элементами (такими как термопары, болометры и термоиндикаторы). Эти элементы преобразуют параметры поля, такие как температура и температурный градиент, в электрический сигнал, который затем передается на регистрирующие устройства (например, тепловизоры) для выявления аномальных температурных зон, свидетельствующих о дефектах.
Тепловой контроль делится на два метода: пассивный и активный. При пассивном методе объект не подвергается воздействию внешних источников энергии, а активный метод включает воздействие внешних источников тепла на объект.
Методика контроля пассивным методом:
Особенности пассивного метода:
Этот метод проводится бесконтактным способом, с использованием тепловизоров на расстоянии от 2 до 100 м, в зависимости от размера объекта и предполагаемых дефектов. Тепловой контроль не нарушает эксплуатационные качества объекта, обладает высокой мобильностью и информативностью.
Тепловой контроль применяется при производстве, монтаже, ремонте и эксплуатации различных технических устройств и сооружений, включая архитектурные конструкции, дымовые и вентиляционные трубы.
Рекомендуется проводить контроль в условиях минимального воздействия окружающей среды — в ночное время или в облачные дни, когда влияние внешних температурных факторов минимально. Контроль не проводится в условиях дождя, снега или сильного ветра.
Методика контроля активным методом:
Особенности активного метода:
Этот метод может быть проведен как контактным (с использованием термометров и термопар), так и бесконтактным способом, используя тепловизоры и пирометры. Для максимальной точности контроля важно устранить фоновое излучение и загрязнения на поверхности объекта. Метод не нарушает эксплуатационные качества объекта и дает высококачественные результаты.
Тепловой контроль активно используется для диагностики и оценки технического состояния объектов, что позволяет заранее выявить скрытые дефекты, минимизируя риск аварий и поломок.
Принцип работы метода основан на взаимодействии теплового поля объекта с чувствительными термометрическими элементами (такими как термопары, болометры и термоиндикаторы). Эти элементы преобразуют параметры поля, такие как температура и температурный градиент, в электрический сигнал, который затем передается на регистрирующие устройства (например, тепловизоры) для выявления аномальных температурных зон, свидетельствующих о дефектах.
Тепловой контроль делится на два метода: пассивный и активный. При пассивном методе объект не подвергается воздействию внешних источников энергии, а активный метод включает воздействие внешних источников тепла на объект.
Методика контроля пассивным методом:
- Оценка условий эксплуатации объекта.
- Изучение расположения объекта и факторов, которые могут повлиять на результаты контроля.
- Анализ метеорологических и технологических параметров, а также окружения объекта.
- Настройка тепловизора и выбор оптимального положения для съемки.
- Проведение тепловизионной съемки объекта.
- Интерпретация результатов контроля.
Особенности пассивного метода:
Этот метод проводится бесконтактным способом, с использованием тепловизоров на расстоянии от 2 до 100 м, в зависимости от размера объекта и предполагаемых дефектов. Тепловой контроль не нарушает эксплуатационные качества объекта, обладает высокой мобильностью и информативностью.
Тепловой контроль применяется при производстве, монтаже, ремонте и эксплуатации различных технических устройств и сооружений, включая архитектурные конструкции, дымовые и вентиляционные трубы.
Рекомендуется проводить контроль в условиях минимального воздействия окружающей среды — в ночное время или в облачные дни, когда влияние внешних температурных факторов минимально. Контроль не проводится в условиях дождя, снега или сильного ветра.
Методика контроля активным методом:
- Подготовка поверхности объекта — очистка от загрязнений.
- Установка контролируемого объекта и необходимого оборудования.
- Нанесение термоиндикаторов или установка термометров и термопар.
- Нагрев объекта до необходимой температуры или подача теплового импульса.
- Наблюдение и измерение параметров.
- Оценка полученных данных.
Особенности активного метода:
Этот метод может быть проведен как контактным (с использованием термометров и термопар), так и бесконтактным способом, используя тепловизоры и пирометры. Для максимальной точности контроля важно устранить фоновое излучение и загрязнения на поверхности объекта. Метод не нарушает эксплуатационные качества объекта и дает высококачественные результаты.
Тепловой контроль активно используется для диагностики и оценки технического состояния объектов, что позволяет заранее выявить скрытые дефекты, минимизируя риск аварий и поломок.
Металлографические исследования (металлография)
Металлографические исследования являются важным инструментом для анализа структуры основного металла и сварных соединений. Они позволяют выявить внутренние дефекты, такие как трещины, непровары, пористость и другие повреждения, а также оценить структуру материала, использованного в сварке (низкоуглеродистые, низколегированные, среднелегированные, высоколегированные стали и цветные металлы, такие как медь, алюминий, титан и серебро). Этот метод широко применяется при исследовании причин разрушений деталей машин, аппаратов, а также элементов металлических конструкций.
Металлографическое исследование включает в себя как макро-, так и микроструктурный анализ:
Металлографические исследования могут быть как разрушающими, так и неразрушающими.
Разрушающая металлография предполагает вырезку образца из объекта контроля для дальнейшего исследования его структуры под микроскопом. Этот метод используется для детального изучения состояния материала, но нарушает целостность исследуемого объекта.
Неразрушающая металлография включает два метода:
Принцип работы этих методов заключается в применении оптических микроскопов для исследования структуры металла при увеличении от 20 до 2000 раз. Для оценки результатов сравниваются полученные данные с эталонными шкалами в соответствии с соответствующими стандартами (ГОСТ).
Методика контроля с разрушающим методом:
Особенности разрушающего метода:
Этот метод позволяет обнаружить изменения в структуре металла, которые могут привести к снижению прочности материала и, как следствие, ухудшению прочности всей конструкции. Однако, данный метод нарушает целостность объекта, что требует проведения восстановительного ремонта после исследования.
Металлографические исследования применяются в различных областях, включая нефтехимию, энергетику и машиностроение, для анализа причин повреждений оборудования и сварных соединений. Эти исследования также необходимы для определения остаточного ресурса технологического оборудования.
Методика неразрушающего контроля с методом реплик:
Методика неразрушающего контроля с портативным микроскопом:
Особенности неразрушающего метода:
Этот метод позволяет проводить анализ без нарушения целостности объекта. Однако его применение может быть затруднено в случае труднодоступности объектов или сложности подготовки шлифов на месте.
Металлографическое исследование включает в себя как макро-, так и микроструктурный анализ:
- Макроструктурный анализ позволяет определить форму, размеры шва, наличие крупных дефектов, таких как трещины, шлаковые включения и усадочные рыхлости.
- Микроструктурный анализ фокусируется на более мелких дефектах, таких как газовые поры, окисные пленки, микротрещины и загрязнения в шве, связанные с неметаллическими включениями.
Металлографические исследования могут быть как разрушающими, так и неразрушающими.
Разрушающая металлография предполагает вырезку образца из объекта контроля для дальнейшего исследования его структуры под микроскопом. Этот метод используется для детального изучения состояния материала, но нарушает целостность исследуемого объекта.
Неразрушающая металлография включает два метода:
- Метод реплик, при котором с зашлифованной поверхности металла снимается слепок (реплика) для дальнейшего анализа.
- Метод металлографии на объекте, при котором структура исследуется непосредственно на объекте с использованием переносного металлографического микроскопа.
Принцип работы этих методов заключается в применении оптических микроскопов для исследования структуры металла при увеличении от 20 до 2000 раз. Для оценки результатов сравниваются полученные данные с эталонными шкалами в соответствии с соответствующими стандартами (ГОСТ).
Методика контроля с разрушающим методом:
- Вырезка образцов из объекта для подготовки шлифов.
- Шлифовка и полировка для получения шлифов.
- Исследования структуры с использованием стационарного микроскопа с необходимым увеличением.
- Травление шлифа раствором азотной кислоты.
- Фотографирование микроструктуры и оценка с использованием эталонных шкал.
- Интерпретация полученных результатов.
Особенности разрушающего метода:
Этот метод позволяет обнаружить изменения в структуре металла, которые могут привести к снижению прочности материала и, как следствие, ухудшению прочности всей конструкции. Однако, данный метод нарушает целостность объекта, что требует проведения восстановительного ремонта после исследования.
Металлографические исследования применяются в различных областях, включая нефтехимию, энергетику и машиностроение, для анализа причин повреждений оборудования и сварных соединений. Эти исследования также необходимы для определения остаточного ресурса технологического оборудования.
Методика неразрушающего контроля с методом реплик:
- Подготовка шлифа на объекте.
- Шлифовка и полировка для подготовки шлифа.
- Травление с использованием азотной кислоты.
- Снятие реплики с полистирола, смоченного в бензоле.
- Исследование микроструктуры с использованием стационарного микроскопа.
- Оценка результатов с использованием эталонных шкал.
Методика неразрушающего контроля с портативным микроскопом:
- Подготовка шлифа непосредственно на объекте.
- Шлифовка и полировка.
- Травление шлифа.
- Исследование с помощью портативного микроскопа прямо на объекте.
- Оценка с использованием эталонных шкал.
Особенности неразрушающего метода:
Этот метод позволяет проводить анализ без нарушения целостности объекта. Однако его применение может быть затруднено в случае труднодоступности объектов или сложности подготовки шлифов на месте.
Радиационный контроль
Процесс радиационного контроля обычно включает схожую последовательность действий для всех его типов. Ионизирующее излучение проходит через объект контроля и фиксируется специальным детектором, таким как рентгеновская пленка или флуоресцирующий экран. Наиболее распространенными методами являются рентгенография (или радиография) и гаммаграфия.
Рассмотрим основные этапы радиационного контроля на примере рентгенографии:
Рентгенографический контроль, благодаря своей эффективности в выявлении практически всех видов дефектов, является обязательным в ряде случаев, указанных в строительных нормах и правилах, например, СНиП 3-05-05-84 "Технологическое оборудование и технологические трубопроводы" и СНиП III-42-80 "Магистральные трубопроводы". Оборудование для радиационного контроля может сильно различаться по характеристикам.
Рассмотрим основные этапы радиационного контроля на примере рентгенографии:
- Подготовка поверхности — очистка от брызг металла, неровностей и инородных объектов, которые могут помешать качественному анализу снимков.
- Установка источника излучения — размещение рентгеновского источника, эталонов чувствительности (для оценки качества контроля) и принимающего экрана (например, рентгеновской пленки).
- Процесс просвечивания — объект подвергается рентгеновскому излучению.
- Проявление снимков — фотографические изображения проявляются в специальной комнате с использованием осветителей, таких как негатоскопы.
- Интерпретация снимков — расшифровка полученных изображений для выявления возможных дефектов.
Рентгенографический контроль, благодаря своей эффективности в выявлении практически всех видов дефектов, является обязательным в ряде случаев, указанных в строительных нормах и правилах, например, СНиП 3-05-05-84 "Технологическое оборудование и технологические трубопроводы" и СНиП III-42-80 "Магистральные трубопроводы". Оборудование для радиационного контроля может сильно различаться по характеристикам.
Как это работает на самом деле
На предприятиях часто бывает нецелесообразно использовать сложные методы испытаний для контроля качества сварки металлов в простых конструкциях. В таких случаях достаточно применять базовые неразрушающие методы, такие как визуально-измерительный и капиллярный контроль. Эти процедуры обычно выполняются мастером или бригадиром, и если работу выполняет опытный сварщик, то в основном полагаются на его знания и навыки. Данные методы не требуют значительных затрат на оборудование, а также дополнительных углубленных знаний о материалах от персонала.
Однако когда требования к прочности сварных соединений повышены, например, в соответствии с технической документацией объекта, требуется более тщательная проверка качества швов с экспертным заключением дефектоскописта. В таких случаях без заключения специалиста не удастся подписать акт приёмки-сдачи детали, узла или конструкции. Для выполнения таких проверок организации обращаются в сертифицированные лаборатории. В зависимости от условий, типа объекта, марок и толщины свариваемых сталей выбирается соответствующий метод контроля. После согласования всех деталей составляется план работы и подписывается договор.
Однако когда требования к прочности сварных соединений повышены, например, в соответствии с технической документацией объекта, требуется более тщательная проверка качества швов с экспертным заключением дефектоскописта. В таких случаях без заключения специалиста не удастся подписать акт приёмки-сдачи детали, узла или конструкции. Для выполнения таких проверок организации обращаются в сертифицированные лаборатории. В зависимости от условий, типа объекта, марок и толщины свариваемых сталей выбирается соответствующий метод контроля. После согласования всех деталей составляется план работы и подписывается договор.