Сосуды, функционирующие под избыточным давлением, представляют собой объекты повышенного риска, эксплуатация которых требует особого внимания и строгого контроля. Даже незначительные отклонения в состоянии их стенок или соединений способны привести к тяжёлым технологическим сбоям, угрозе жизни персонала и значительным материальным потерям.
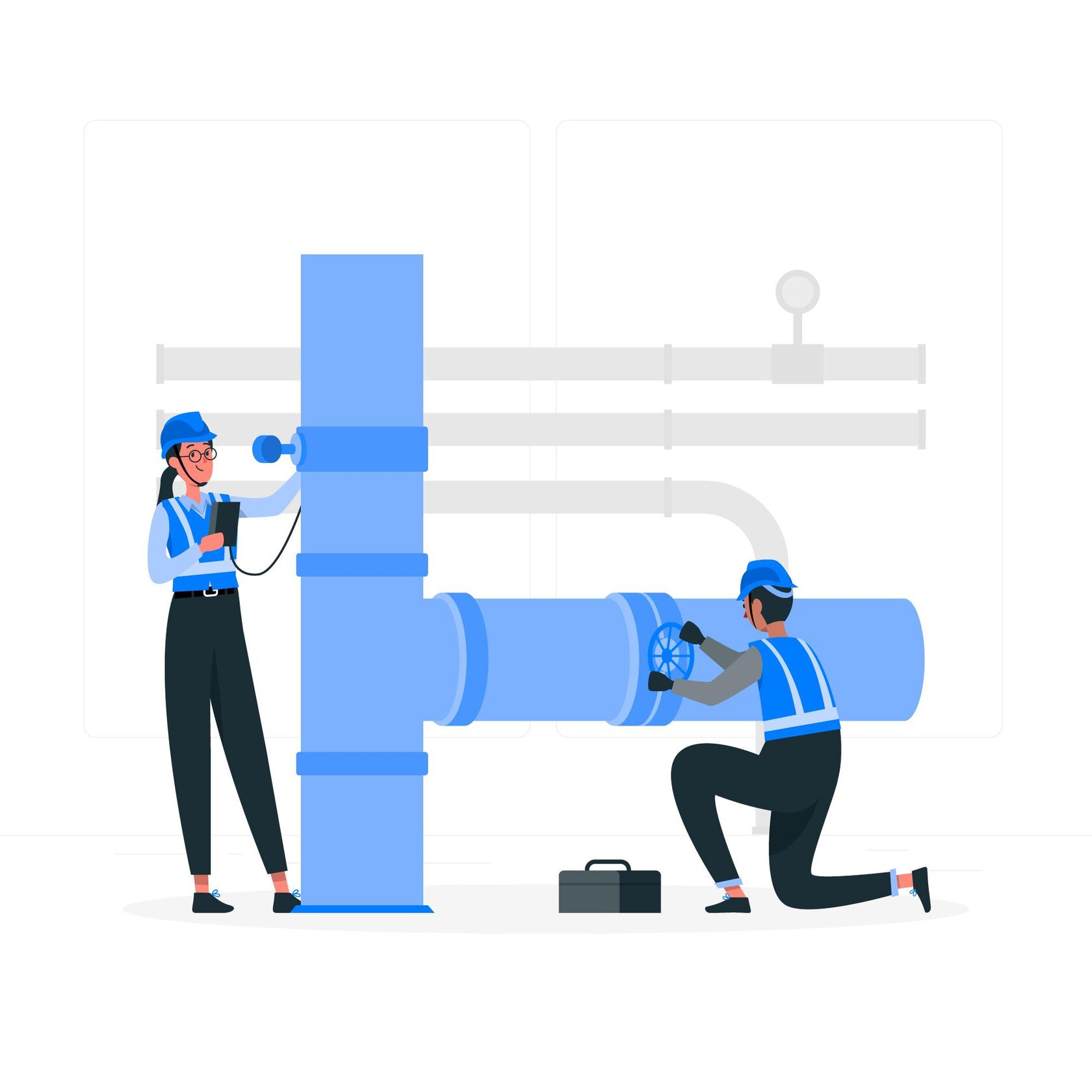
В этой связи гидравлические испытания выступают ключевым этапом оценки технического состояния оборудования — как перед первым запуском, так и в процессе эксплуатации. Их основная задача — убедиться в прочности конструкции, отсутствии утечек и полном соответствии установленным стандартам безопасности.
Гидравлические испытания сосудов, работающих под избыточным давлением
Оценка прочности и герметичности сосудов, функционирующих в условиях избыточного давления, осуществляется посредством гидравлических испытаний — обязательной процедуры, направленной на обеспечение безопасности эксплуатации оборудования. Основным нормативным документом, регламентирующим порядок проведения испытаний, выступает РД 24.200.11-90. Работы выполняются исключительно квалифицированными специалистами, имеющими соответствующую аттестацию и использующими поверенные измерительные приборы.
Процедура испытаний сопровождается строгим соблюдением технических требований:
- Контрольное давление не должно превышать 125 % от рабочего, а для сосудов с параметрами до 0,05 МПа превышение номинала категорически запрещено.
- Визуальный осмотр осуществляется как при номинальном, так и при повышенном давлении.
- К испытаниям не допускаются резервуары с признаками значительного износа, механическими повреждениями или следами некачественного ремонта.
- Также запрещена проверка сосудов, конструкционная надежность или качество монтажа которых вызывает сомнения.
Нормативное регулирование гидравлических испытаний сосудов, работающих под давлением
Проведение гидравлических испытаний сосудов, эксплуатируемых в условиях избыточного давления, строго регламентируется комплексом нормативно-правовых актов. Эти документы определяют технические требования к методике испытаний, параметрам оборудования и материалов, а также предусматривают меры ответственности за нарушение установленных стандартов. Надлежащая правовая база обеспечивает единообразие процедур и высокую степень промышленной безопасности.
- ГОСТ Р 52630-2012 «Методы контроля сосудов и аппаратов». Стандарт определяет порядок выполнения гидравлических испытаний, включая методику расчёта пробного давления и допустимых предельных значений. Документ применяется при проектировании, изготовлении, техническом обслуживании и контроле состояния оборудования.
- РД 24.200.11-90 «Сосуды и аппараты, работающие под давлением. Правила и нормы безопасности при проведении гидравлических испытаний на прочность и герметичность». Данный нормативный документ регламентирует порядок обеспечения безопасности при проведении гидравлических испытаний сосудов и аппаратов, функционирующих под давлением. Он содержит обязательные требования к подготовке и выполнению проверок на прочность и герметичность, распространяющиеся на оборудование, изготавливаемое в соответствии с положениями следующих отраслевых стандартов: ОСТ 26-291, ОСТ 26-01-1183, ОСТ 26-01-900, ОСТ 26-11-06, ОСТ 26-18-6, ОСТ 26-01-9 и ОСТ 26-01-221.
- Приказ Ростехнадзора от 15.12.2020 № 536 «Об утверждении федеральных норм и правил в области промышленной безопасности „Правила промышленной безопасности при использовании оборудования, работающего под избыточным давлением“». Этот нормативный акт регулирует весь жизненный цикл сосудов под давлением — от ввода в эксплуатацию до вывода из обращения. В числе прочего, он содержит требования к периодическим испытаниям и освидетельствованию, а также к ведению технической документации.
Так же, стоит отметить ГОСТ 14249-89 Сосуды и аппараты. Нормы и методы расчета на прочность.
Диагностике подлежат следующие виды оборудования:
Допускается испытание других видов резервуаров, если это обусловлено их конструктивными особенностями и условиями эксплуатации.
Частота проведения испытаний определяется категорией сосуда. Для изделий I и II категории диагностика обязательна при вводе в эксплуатацию, по завершении ремонта или после длительного простоя (более двух лет). В период штатного использования испытания повторяются с периодичностью от 2 до 8 лет, в зависимости от внутреннего регламента предприятия. Для сосудов III категории испытания проводятся только перед первым запуском и после ремонтных мероприятий, без необходимости в периодическом контроле.
- теплообменные аппараты различных типов;
- испарительные емкости;
- баллоны для хранения газов под давлением или в сжиженном виде;
- резервуары, используемые при обращении с нефтепродуктами;
- сосуды, предназначенные для горячей воды и водяного пара, функционирующие при давлении свыше 0,07 МПа и температуре до 115 °C.
Допускается испытание других видов резервуаров, если это обусловлено их конструктивными особенностями и условиями эксплуатации.
Частота проведения испытаний определяется категорией сосуда. Для изделий I и II категории диагностика обязательна при вводе в эксплуатацию, по завершении ремонта или после длительного простоя (более двух лет). В период штатного использования испытания повторяются с периодичностью от 2 до 8 лет, в зависимости от внутреннего регламента предприятия. Для сосудов III категории испытания проводятся только перед первым запуском и после ремонтных мероприятий, без необходимости в периодическом контроле.
Определение пробного давления
Для обеспечения безопасности и точности гидроиспытаний необходимо правильно рассчитать пробное давление — величину нагрузки, при которой проверяется прочность и герметичность оборудования.
Таблица расчёта пробного давления сосудов
Обозначения:
P — рабочее давление, МПа
Pпр — пробное давление, МПа
[σ]20 — допускаемое напряжение при 20 °C
[σ]t — допускаемое напряжение при расчётной температуре
Km — доля металла в конструкции
α — коэффициент, зависящий от ударной вязкости
P — рабочее давление, МПа
Pпр — пробное давление, МПа
[σ]20 — допускаемое напряжение при 20 °C
[σ]t — допускаемое напряжение при расчётной температуре
Km — доля металла в конструкции
α — коэффициент, зависящий от ударной вязкости
Подготовительный этап к гидравлическим испытаниям сосудов, работающих под давлением
Подготовка к проведению гидравлических испытаний сосудов, эксплуатируемых под избыточным давлением, представляет собой многоэтапный процесс, от которого напрямую зависит точность диагностических результатов и безопасность всех участников работ. Каждый шаг требует строгого соблюдения технических норм и организационной дисциплины.
Комплексная подготовка документации
Перед началом испытательных мероприятий необходимо сформировать полный пакет сопроводительных материалов:
- Проектная и эксплуатационная документация: чертежи, спецификации, паспортные данные и схемы узлов сосуда.
- Методики испытаний: включая ссылки на применимые нормативы и внутренние регламенты организации.
- Акты и протоколы предыдущих проверок: используются для анализа динамики состояния оборудования и выявления возможных тенденций к износу.
Визуальное обследование оборудования
До заполнения сосуда тестовой жидкостью проводится внешний осмотр с целью исключения дефектов, которые могут повлиять на результаты или сделать испытание небезопасным:
- Проверяются сварные соединения на наличие дефектов (трещин, раковин, следов перегрева).
- Оценивается внешняя поверхность на предмет вмятин, коррозионных участков и механических повреждений.
- При доступе к внутреннему пространству выполняется осмотр изнутри — в первую очередь на наличие загрязнений, налёта, следов усталости металла.
Очистка испытательной ёмкости
Перед началом испытаний сосуд подлежит полной очистке от всех видов загрязнений:
- Механическая обработка: удаление твёрдых отложений, продуктов коррозии и технологического мусора.
- Химическая промывка: применяется для удаления масложировых загрязнений.
- Продувка инертным газом или воздухом: удаление остатков жидкости и мелкодисперсных примесей.
Подготовка рабочей жидкости
В большинстве случаев в качестве среды используется вода, однако в особых условиях (например, при низких температурах) допустимо применение других жидкостей:
- Контроль качества: испытательная жидкость должна быть нейтральной, без агрессивных примесей и взвесей.
- Температурный режим: жидкость должна иметь температуру, максимально приближенную к температуре окружающей среды во избежание температурного расширения металла.
Проверка технического оснащения
Вся аппаратура и измерительные средства, задействованные в испытаниях, проходят предварительную проверку:
- Манометры: калибруются и сверяются с эталонными приборами.
- Гидравлические агрегаты: должны обеспечивать плавный и равномерный набор давления.
- Запорная арматура и предохранительные клапаны: проходят тест на герметичность и функциональность.
Организация и защита рабочей зоны
Перед проведением испытаний подготавливается площадка с учетом требований охраны труда и промышленной безопасности:
- Устанавливаются ограждения, запрещающие доступ посторонних.
- Все участники обеспечиваются средствами индивидуальной защиты (каски, очки, защитные перчатки и обувь).
- Готовятся аварийные средства: системы аварийного сброса давления, сигнализации и связи.
Заполнение сосуда жидкостью
Завершающий этап подготовки — аккуратное и постепенное наполнение резервуара:
- Плавное заполнение исключает резкие перепады давления и гидроудары.
- Удаление воздуха осуществляется через специальные клапаны или вентили, поскольку наличие воздушных пробок искажает показания и повышает риски.
Каждый из этапов подготовки строго регламентирован и должен выполняться в соответствии с действующими нормативами. Игнорирование отдельных пунктов может привести к недостоверным результатам испытаний или создать угрозу аварийной ситуации.
Этапы проведения комплексных гидравлических испытаний сосудов под давлением
Комплексная проверка сосудов, предназначенных для работы под избыточным давлением, представляет собой регламентированную процедуру, включающую в себя последовательность диагностических этапов, направленных на подтверждение их эксплуатационной надёжности и соответствия установленным требованиям безопасности.
Первичный визуально-измерительный контроль
Испытания начинаются с тщательной проверки физического состояния оборудования:
- Проверяется геометрия корпуса, соответствие размерам, допустимым по чертежам;
- Обнаруживаются механические повреждения, вмятины, деформации, следы агрессивной коррозии;
- При необходимости проводится измерение толщины стенок в критических участках;
- Оцениваются признаки несанкционированного ремонта или усталостных деформаций.
Применение методов неразрушающего контроля
Для дополнительной оценки сварных соединений используются специальные методы технической диагностики:
- Ультразвуковой контроль — позволяет выявить внутренние непровары, расслоения и пустоты;
- Радиографический анализ (рентгенография) — обеспечивает визуализацию дефектов в теле шва;
- Капиллярная дефектоскопия — применяется для обнаружения поверхностных трещин и пор.
Испытание на прочностные характеристики
На этом этапе проводится проверка способности сосуда выдерживать избыточное давление без потери конструктивной целостности:
- Давление подаётся с превышением расчетного рабочего значения — обычно на 25–50% выше нормы, в соответствии с заданным коэффициентом безопасности;
- Корпус, швы и фланцевые соединения не должны демонстрировать остаточной деформации;
- Любые признаки утонения, вспучивания или протечки недопустимы.
Контроль герметичности
Задача — удостовериться, что внутренняя среда сосуда не проникает наружу при рабочем или повышенном давлении:
- Применяется пневматическое или гидравлическое воздействие, в зависимости от условий испытания;
- Давление повышается ступенчато и выдерживается на каждом этапе в течение установленного времени;
- Падение давления, образование влажных пятен или испарений — основание для признания сосуда негерметичным.
Проведение гидравлических испытаний
Этот метод является базовым для контроля прочности и герметичности:
- Внутренняя полость заполняется технически чистой водой, температура которой контролируется, чтобы избежать термического напряжения;
- Давление создаётся с помощью сертифицированного насосного оборудования, снабжённого манометрическими приборами и аварийной арматурой;
- Визуальный контроль осуществляется непрерывно — отслеживаются корпус, сварные швы, резьбовые и фланцевые соединения.
Фиксация результатов
По завершении испытаний составляется официальный протокол, отражающий:
- Фактически достигнутое давление и его удержание;
- Продолжительность испытания;
- Результаты внешнего осмотра;
- Заключение о пригодности оборудования к дальнейшей эксплуатации.
Этот протокол входит в состав технической документации сосуда и подлежит обязательному хранению. Он предъявляется при сертификационных проверках, технических аудитах и контроле со стороны надзорных инстанций.
Заключительным этапом проведения гидравлических испытаний сосудов и аппаратов под давлением является оформление акта испытаний, который служит официальным подтверждением их технической пригодности. Этот документ не только фиксирует все параметры, полученные в ходе проверки (давление, продолжительность, результаты осмотра), но и удостоверяет соответствие оборудования установленным нормам безопасности. Акт оформляется в соответствии с требованиями ВСН 478-86 и имеет юридическую силу при вводе оборудования в эксплуатацию, а также при проведении надзорных проверок. От полноты и точности его составления зависит возможность дальнейшего безопасного использования сосудов и аппаратов в производственных процессах.
Производственная документация по монтажу технологического оборудования и технологических трубопроводов. ВСН 478-86 (утв. Минмонтажспецстроем СССР 18.03.86)
Скачать образец Акт испытания сосудов и аппаратов.
Соблюдение всех этапов испытаний в полном объёме обеспечивает не только достоверную оценку технического состояния оборудования, но и предотвращает риски, связанные с его потенциальной неисправностью при последующей эксплуатации.